Understanding Common Cut
In traditional nesting, a standard gap is maintained between parts to prevent damage during cutting. In Nest&Cut, this gap is referred to as the “part gap.”
However, there’s a more efficient approach. The common cut technique eliminates unnecessary gaps by setting the spacing between parts to match the exact diameter of the cutting tool, known as the kerf in Nest&Cut. This enables a single pass of the tool to cut along shared edges, streamlining the cutting process.
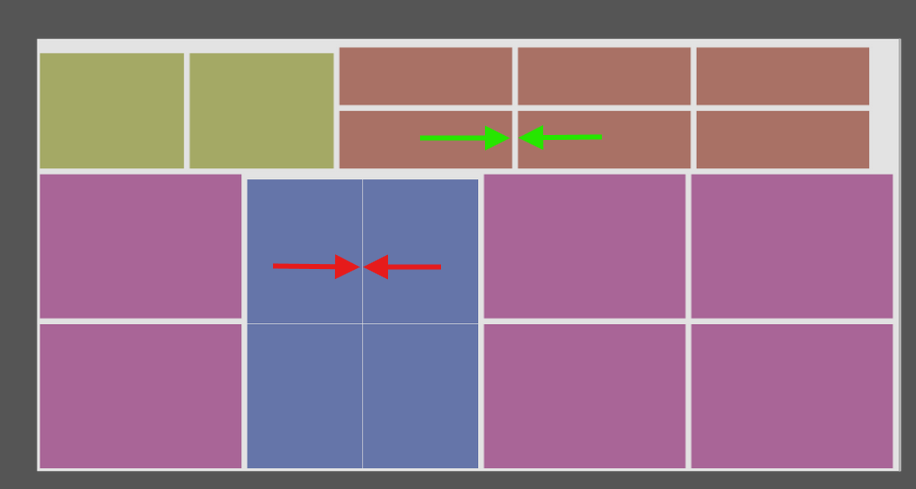
In green the standard part gap (typically 5 mm in laser), in red the common cut gap which is chosen equal to the kerf (the diameter of the cutting tool, typically 0.1 mm in laser
Visualizing Common Cut
- Standard Part Gap: Typically set at 5mm for laser cutting, ensuring separation between parts.
- Common Cut Gap: Set equal to the kerf (e.g., 0.1mm for laser cutting), allowing shared edges to be cut in one pass.
The benefits of common cut apply to various nesting patterns, including rectangular and non-rectangular parts, as demonstrated in the illustrations provided
![]() With the common cut |
![]() Without the common cut |
Any type of matrix can be cut in common cut:
![]() With the common cut |
![]() Without the common cut |
The Advantages of Common Cut
Implementing common cut in your cutting process offers substantial benefits:
- Reduced Cutting Time: Minimize unnecessary cuts and significantly shorten processing time.
- Lower Tool Wear and Supply Costs: Decrease tool wear by reducing total cutting distance, leading to cost savings on consumables.
- Material Savings: Optimize material usage and reduce waste.
For instance, in this example on Nest&Cut we get
- 15% reduction in cutting distance (156 meters saved)
- 1.3% less material usage
- Savings of approximately €227 per batch
- 4 hours saved per 27-hour cutting process
![]() With common cut |
![]() Without common cut |
In larger matrices, reductions in cutting length can approach 50%, further amplifying these benefits.
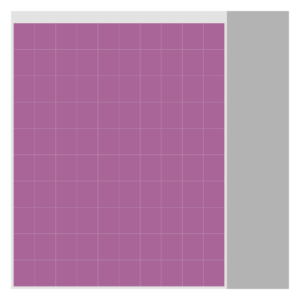
In big matrices of parts such as this one the reduction in cutting length can approach 50%
Activating Common Cut in Nest&Cut
Nest&Cut makes enabling common cut simple with a one-click activation feature. However, behind the scenes, an advanced nesting algorithm ensures the generated layouts are optimal for clean, efficient cutting. The trajectory planning system minimizes lead-ins and ensures smooth operation while avoiding detached pieces.
To activate common cut:
1. Click the Common Cut option in Nest&Cut.
2. Enter the precise kerf value (cutting beam width) to ensure accurate part dimensions
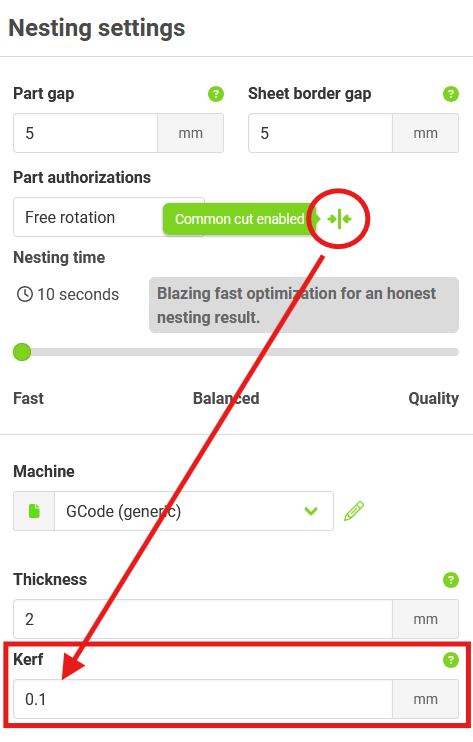
How to enable the common cut in Nest&Cut. Do not forget to provide the kerf (width of the beam) !
Common Cut Handling in DXF and NC Code
- Standard DXF Output: parts are placed at common cut distances while keeping all contours intact.
- NC Machine Output: shared contours are merged, ensuring a single cutting pass between parts in common cut.
- Merged DXF Output: if you require merged contours in a DXF file, select the CAM DXF option when exporting.
Share Your Feedback
While our team has spent over a decade refining common cut algorithms, this feature is newly integrated into Nest&Cut. We value your feedback and invite you to share your experience to help us continue improving this powerful tool.
Start optimizing your nesting process today with common cut in Nest&Cut!