How Stopp optimises companies’ production as an expert composite subcontractor.
Interview with Stéphane Wannyn, STOPP Composites.
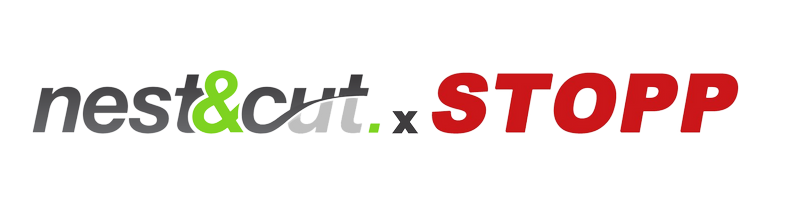
Discovering STOPP Composites.
STOPP Composites was founded in 1976 and is a VSE specialized in the distribution of technical solutions for cutting and assembling technical parts, mainly in the field of composite materials.
STOPP Composites teams work closely with its customers, marketing professional tools for cutting technical fabrics such as scissors, electric or pneumatic hand-held machines, as well as Novex® numerical control cutting tables from Gunnar, Switzerland.
STOPP Composites, as a service provider for the cutting of dry fabrics, glass, carbon, Kevlar® and carbon/epoxy prepregs, organizes all productions from Nest&Cut to generate dxf’s that are then taken over by our Novex® cutting machines.
STOPP Composites applications are wide-ranging: its customers include industrialists in the fields of railways, sanitary, racing cars, sport & leisure and in the nautical industry, as well as equipment manufacturers for public works, agricultural or even mining machinery.
What are the benefits for STOPP Composites’ customers when using subcontracting services?
Customers who use STOPP Composites’ subcontracting services are looking for a long-term partner equipped with precise cutting machines such as Novex®, in order to avoid purchasing their own cutting machine – not necessary when volumes are not large enough to justify such an expense.
They may also be companies that prefer outsourcing because their activity is too fluctuating or seasonal, but still need to move up from traditional hand cutting or handheld machines. Here again, they find STOPP Composites is a partner who will expertly handle the cutting part of their operations.
Our customers are also attracted to subcontracting for a number of reasons: they need a finer production management that will adapt the cutting station to their own production volumes, without having to transfer a team to other tasks, if their activity is reduced for a time. Another important criterion for Stéphane Wannyn of STOPP Composites is the reduction of MSD (musculoskeletal disorders): Cutting with scissors, and even with a hand-held cutting machine – on a daily basis and for several hours – increases the risk of RSI for operators when handling very thick fabrics that can sometimes reach up to 2 kg/m2.
What about Nest&Cut in all this?
The Nest&Cut automatic nesting web application, coupled with Gunnar’s Novex® cutting machines, offers a considerable advantage in terms of material waste savings.
Customers are also increasingly sensitive to environmental issues regarding waste management. Recycling or reducing waste is a significant cost-saving benefit, indeed, but also has a positive impact on the environment. Dumping glass and carbon fabrics in landfills has a significant cost and ecological
impact. To date, they do not return to the industry and are not recycled. The optimal nesting of parts therefore brings undeniable added value.
The use of nesting software such as Nest&Cut has become a necessity for STOPP Composites in parallel with digital cutting machines marketing. Initially, Nest&Cut was used on an ad hoc basis, for economic reasons and convenience.
Nest&Cut offers the flexibility of a tool with reasonable cost management. Very quickly, Nest&Cut proved to be an intuitive tool for STOPP Composites, well-suited to composite parts management. Indeed, fiber orientations management or the positioning of fabrics for example are criteria that Nest&Cut must and can meet.
Automating most of Nest&Cut’s functions is also an added asset. One of the features Stéphane Wannyn appreciates in Nest&Cut is its ability to check DXF files from the start, thanks to automatic cleaning. We save a lot of time when nesting parts that cannot be matched because of open contours, for example.
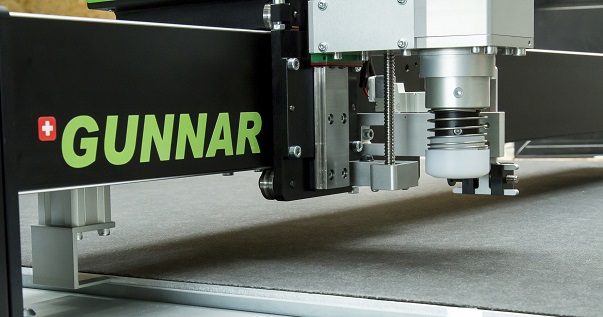
How has Nest&Cut been adopted on a daily basis by STOPP Composites?
Adoption by the team was quick as it is easy to get the hang of it. There are enough options in Nest&Cut to fit our business while being easy and fast. Specifically, STOPP Composites retrieves its customers’ more or less complete DXF files from 2D CAD software and processes them with Nest&Cut. Once they are clean, we nest them and recover a “nested” file in DXF format that can be used directly with our Novex® machines.
Indeed, since STOPP Composites can know their cutting times according to fabrics, just like a sheet metal manufacturer (who knows processing durations according to its sheets thickness and therefore uses laser cutting or jet cutting machines), STOPP Composites‘ teams can easily provide feedback to its customers.
For example, the calculation of part weight, thanks to the workshop sheet, lets them communicate to their customers the total surface area per fabric of the cuttings. This is very helpful for STOPP Composites as they can take only the surface area of the cut parts, which is important information to calculate the final weight of a vehicle in the racing or aeronautics industry, for example.
Ideas to improve the Nest&Cut experience.
STOPP Composites manages different customers and different fabrics on a daily basis, with specific codes for each fabric. Naming the formats, in addition to fabrics lengths and widths already available in Nest&Cut, would reinforce formats identification (90% of the requests concern similar widths and lengths of identical fabrics). This is another step towards zero defects, because the rigor applied to fabrics identification is essential.